News
Hard-Core Hybrids
Vertiflite | May/June 2021
Fuel-burning engine-generator sets offer choices of efficient power schemes and extended endurance for eVTOL vehicles. This round-up highlights some of the current plans and progress.
Fuel-burning engine-generator sets offer choices of efficient power schemes and extended endurance for eVTOL vehicles. This round-up highlights some of the current plans and progress.
Numerous electric vertical takeoff and landing (eVTOL) designs rely on hybrid electric propulsion to offset the limited power density of current battery technology (see “Halfway to Paradise?” Vertiflite, Sept/Oct 2020). Hybrid-electric solutions now under development maximize design freedom by using reciprocating or turbine engines to drive generator sets to power distributed electric propellers or fans. Hybrid architectures can recharge batteries for quiet flight or battery-augmented takeoffs.
VerdeGo Aero
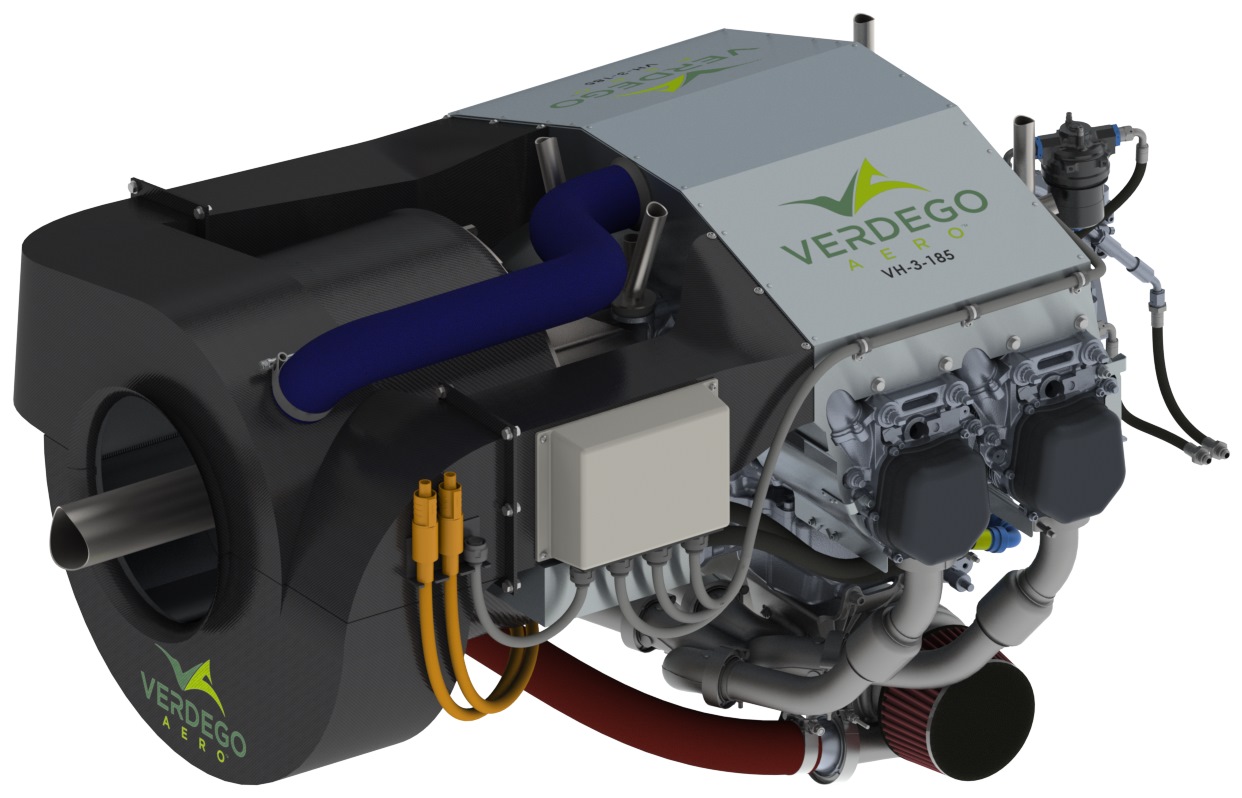
VerdeGo’s VH-3-185 hybrid-electric propulsion package will be available in a direct-drive package or with a mechanical output shaft and clutch to accommodate series and parallel operating modes. (VerdeGo)
In March, VerdeGo Aero in Daytona Beach, Florida, revealed details of its third-generation hybrid-electric propulsion system for serial and parallel applications in electrified aircraft. The VH-3-185 hybrid generator set integrates a modified four-cylinder, 230-hp (170-kW) Röder reciprocating engine with a customized generator/motor, control electronics and cooling systems to provide 185 kW output power. The generator set has a dry weight around 650 lb (295 kg) and can be paired to provide two completely parallel systems with 370 kW combined output. “It positions us in a nice design space where we have a much higher equivalent energy density than the best battery packs on the market,” said VerdeGo Aero CEO Eric Bartsch.
The hybrid-electric propulsion package will be available in a directdrive package or with a mechanical output shaft and clutch. “There are a lot of different operating modes,” noted Bartsch. “The simplest one is to just use it as a source of electrical power and route that power out the bus to motors elsewhere on the aircraft. That’s most common.” Bartsch added, “What we’ve found is there are some customers who have a main propulsion unit, a propeller or a rotor overhead, where a lot of power needs to go… The output shaft could split the power from the piston engine to a main propeller or rotor while the generator powers a distributed electric propulsion array.”
Aircraft designers could shut down the motor and drive the generator with a battery pack alone or draw on combustion engine and battery power simultaneously to provide 370 kW burst power for takeoff and drop down to battery power for greatest cruise efficiency. The new engine-generator set is largely air-cooled but includes a small, self-contained liquid cooling system. “From the airframer’s perspective, it’s an air-cooled system,” explained Bartsch. A purpose-built control system governs the generator, power-distribution electronics and cooling system. “We’re able to deliver very consistent power output [and] maintain consistent voltage with the control architecture we’ve got. What’s important is to have a highly reliable source of energy that can interact well with the battery pack, so you’ve got a fully hybrid system.”
VerdeGo Aero plans to certify the hybrid-electric generator set under US Federal Aviation Regulations (FAR) Part 33 rules governing stand-alone piston and turbine engines. “That obviously simplifies certification of the [customer] aircraft because you’re using a known quantity for the engine.” Current plans begin with the first pre-production units delivered for early-adopter flight testing within 18 months to two years. Low-volume production to support customer flight testing and non-certified applications will run in parallel with US Federal Aviation Administration (FAA) certification testing using fully conformal hardware.
VerdeGo Aero will integrate the new generator sets in its own production facilities at a site to be announced. “We will make the final unit,” said Bartsch. “Röder is the vendor for the diesel engine that’s inside. We have [a research and development] facility now where we’re doing low-volume production.” The VH-3-185 uses the SR305 engine, created by SMA Engines (Société de Motorisations Aéronautiques) in 1997, located in Bourges, France. The company was acquired by Safran in 2005, but sold to Egelsbach, Germany-based Röder Präzision GmbH in September 2020.
VerdeGo Aero found that most electric aircraft programs prioritize lower cost of ownership, reduced noise and better efficiency. “You need a hybrid that can operate quietly,” noted Bartsch. “Small turbines are expensive, loud and burn a lot of gas.” VerdeGo Aero chose a previously aircraft-certified diesel-cycle engine for its attractive power-to-weight ratio and compatibility with common jet fuels. “Of course, this hybrid system is going to be used in the general market for electric aircraft, so emissions are important,” said Bartsch. “Compatibility with jet fuel gives us compatibility with all the biofuel alternatives that are available. We want to be sure future carbon-neutral fuel sources are compatible with the VH-3.”
The VH-3-185 is VerdeGo Aero’s third-generation hybrid generator set, progressing from iron bird research tool to low-volume preproduction system to production and certification hardware. Bartsch said, “You can basically think about it as each time we went forward, we cut the weight and size in half and increased the power output.” The company is working with the FAA defining Part 33 and equivalent requirements.
Bartsch observed, “In order to get the full benefit of a hybridelectric aircraft, it’s important [that] the aircraft design leverage the new powerplant, either with distributed propulsion, active aerodynamics or all manner of things you can do with that electricity.” He noted that retrofits or conversions of traditional aircraft are not terribly attractive markets for hybridization. “You can make it fly and make it work. [But] it doesn’t make the aircraft better… I think a vertical takeoff aircraft where you’ve got eight propulsors instead of one, that’s something you can’t do with conventional propulsion. Those are great examples of where you’d like to have something like the VH-3.”
General Electric
Meanwhile, turboshaft engine manufacturers are also developing solutions for hybrid-electric aircraft. GE Aviation’s Catalyst turboprop engine is nearing flight tests on a modified Beechcraft 350 King Air. Called “the first new, clean-sheet turboprop developed for the Business & General Aviation market in more than 30 years,” the Catalyst can produce 850–1,650 shp (630–1,230 kW). The company has said that installing a permanent magnet generator in lieu of the propeller would create a 1-MW hybrid-electric powerplant for advanced air mobility solutions, such as electric vertical takeoff and landing (eVTOL) aircraft. The Catalyst was selected by XTI Aircraft as the engine for its Trifan 600 (see “XTI Aircraft’s TriFan 600 Development Continues,” Vertiflite, March/April 2020).
Honeywell
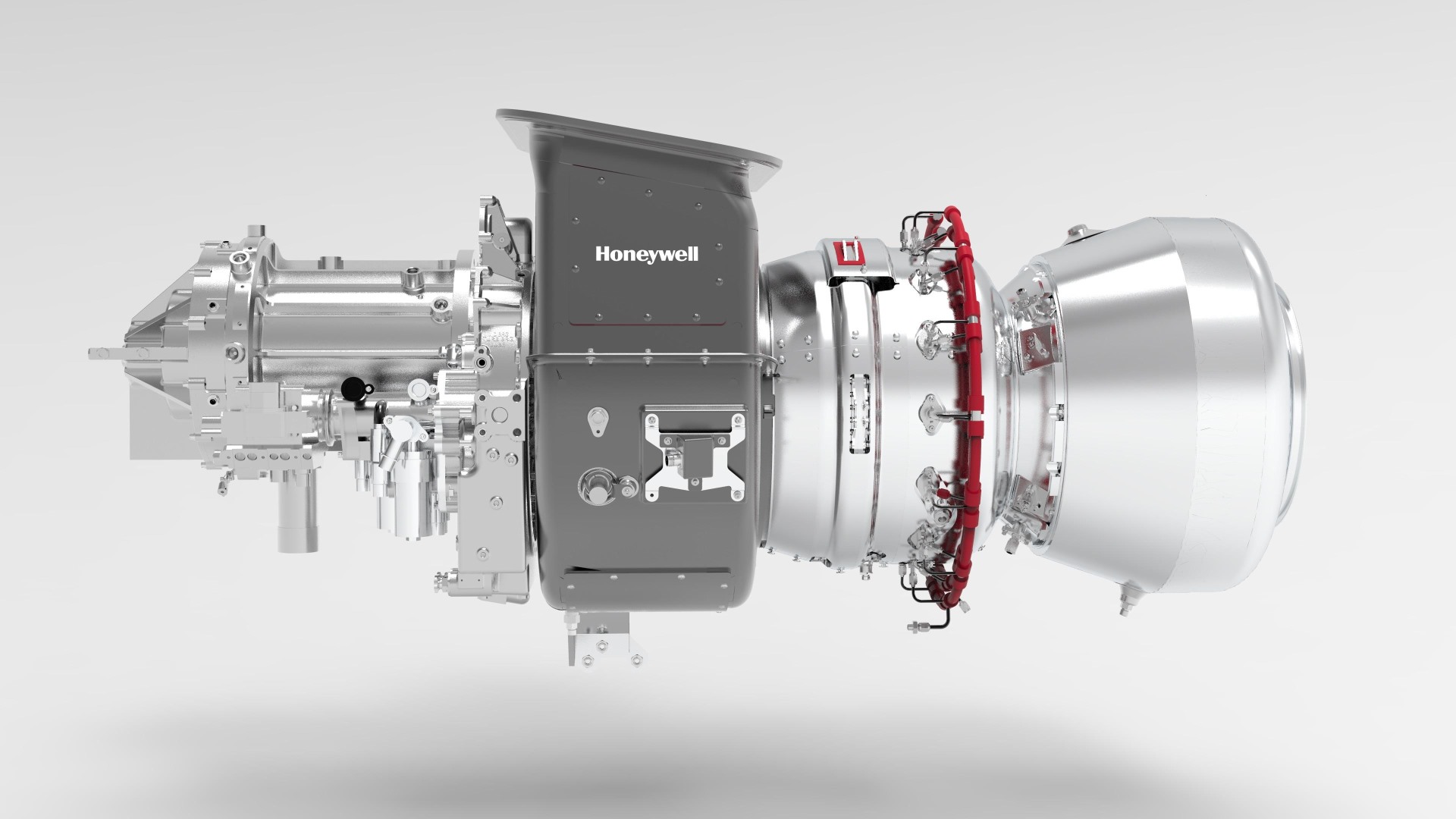
Honeywell announced its 1-MW generator, based on the HGT1700 auxiliary power unit, in March. (Honeywell)
Honeywell Aerospace announced that it is developing a power source for hybrid-electric aircraft, planned for demonstration later this year. “At 280 pounds [127 kg], the Honeywell 1-Megawatt generator weighs about the same as a motor scooter but delivers enough energy to power an entire neighborhood block,” the company said in a March 8 press release. This generator is combined with the Honeywell HGT1700 auxiliary power unit, currently flown on every Airbus A350 XWB, to form a turbogenerator 2.5 times more powerful than the version the company unveiled in 2019. That system was based on the company’s HTS900 engine with two generators, each providing 200 kW of power.
In December, Honeywell signed a memorandum of understanding with British startup Faradair Aerospace to collaborate on systems and a turbo-generation unit that will run on sustainable aviation fuel to power Faradair’s Bio Electric Hybrid Aircraft (BEHA). Faradair intends to deliver 300 hybrid-electric short takeoff and landing (eSTOL) BEHAs into service by 2030. Honeywell says it is in advanced discussions with several other potential turbogenerator customers, working to help define power requirements based on mission profiles required by various manufacturers.
LaunchPoint EPS
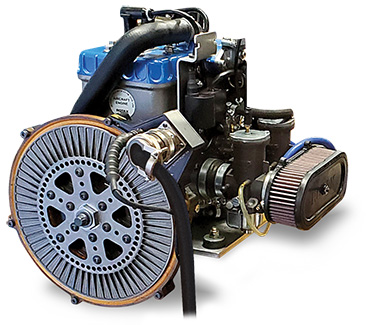
LaunchPoint’s HPS400 uses a Rotax engine to generate 40 kW. (LaunchPoint)
Goleta, California-based LaunchPoint Technologies, which has been developing power-dense Halbach-array electric motors since 2009, spun off a hybrid-electric propulsion company last year. LaunchPoint Electric Propulsion Solutions, Inc., is commercializing the motors, hybrid-electric generator sets and control software developed by LaunchPoint, as well the Modeling Advanced Aircraft Propulsion (MAAP) software, which can be used for designing electric aircraft propulsion systems. LaunchPoint was an Uber Elevate partner; MAAP was developed with support from NASA, Uber Elevate and Elevate-airframe developer, Hyundai.
LaunchPoint EPS is supplying motors and hybrid gensets for electric flight solutions in the unmanned air vehicle, aerospace power generation and advanced air mobility markets. The company originally developed small 6-kW and 40-kW hybridelectric power systems to extend the flight times of unmanned aircraft. It has already supplied several 40-kW HPS400 gensets, based on the Rotax 582 engine, to potential customers.
The company says its patented lightweight, efficient, power dense, air-cooled motors and gensets range from 1.5 kW to 250 kW.
Pratt & Whitney
Like other major engine companies with turboshaft products, Pratt & Whitney Canada is also exploring hybrid-electric solutions. It had planned an ambitious hybrid-electric airliner demonstration under what it called Project 804. Revealed in 2019 under the former United Technologies Advanced Projects (UTAP), it also included Collins Aerospace and Pratt & Whitney Canada, which were then also part of United Technologies Corp., and now all are part of Raytheon Technologies. Project 804 is developing a 1-MW hybrid propulsion system, with the intent to replace one of a De Havilland Canada Dash 8-100’s turboprops.
Raytheon said last summer that the project had been slowed by the COVID-19 pandemic and its impact on civil aviation, which prompted the elimination of some 20,000 jobs across the company.
Rolls-Royce
Rolls-Royce is working with APUS, an aviation engineering company based in Strausberg, close to Berlin, and the Brandenburg University of Technology (BTU) in Cottbus, in developing a hybrid-electric electric conventional takeoff and landing (eCTOL) demonstrator, using Rolls-Royce’s legacy Allison 250 turboshaft. The hybrid-electric M250 could be used across a range of transport platforms to enable distributed electric propulsion, including eVTOL, for power requirements from 500 kW to 1 MW. Rolls-Royce purchased the electric and hybrid-electric aerospace propulsion activities of Siemens in 2019.
Safran and Airbus
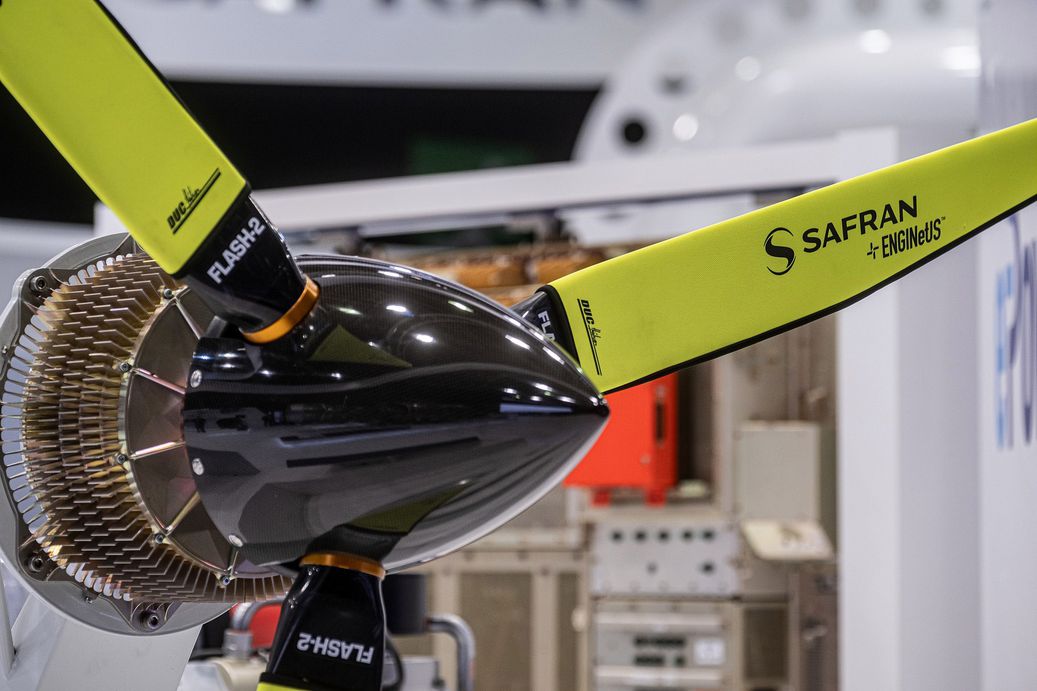
The 50-kW Safran ENGINeUS will be used on the Daher-Safran-Airbus EcoPulse hybrid-electric demonstrator. (Safran)
In July 2018, Safran Helicopter Engines announced it had ground tested its first distributed propulsion system, which generated 100 kW of electrical power, at its facility near Pau-Pyrenees Airport, France. Since then, it has developed a number of technologies for hybrid-electric eVTOL and eSTOL applications.
Safran was selected for Bell’s original hybrid-electric Nexus 6HX eVTOL air taxi, as well as the VoltAero Cassio 1 and the Airbus-Daher EcoPulse Demonstrator eSTOL aircraft. In December, Safran, which is responsible for EcoPulse’s distributed hybridelectric propulsion system, announced it had finalized the technical configuration of its six electric thrusters. They will be fitted with 50 kW ENGINeUS 50 electric motors with integrated electronics and patented air. The Safran ENGINeUS motor will be submitted for certification by the European Union Aviation Safety Agency (EASA) using the same basis as granted for a turboshaft engine. The ENGINeUS 100 will also be certificated by the US FAA on the Bye Aerospace eCTOL eFlyer 2 and eFlyer 4.
Safran is also providing the 2,500-shp (1,860-kW) Aneto-1X engines for the Airbus Racer high-speed compound helicopter. For its “Eco Mode” configuration, one engine can be “paused” and brought to flight idle, for a 15% fuel savings. Whenever needed — during acceleration, landing or autorotation, for example — the idling engine is rapidly and automatically restored to full power using an innovative high-power-density electric motor.
Meanwhile, Airbus provided an update in March on what it calls Europe’s largest facility dedicated to alternative propulsion technologies — its E-Aircraft Systems House, which was launched in 2016. It has two distinct facilities: one for testing mediumvoltage systems appropriate for rotorcraft and eVTOL aircraft, and one for high-voltage testing for larger, commercial aircraft. The medium-voltage facility has been used for the Racer and the CityAirbus eVTOL demonstrator since 2018.
Turbotech
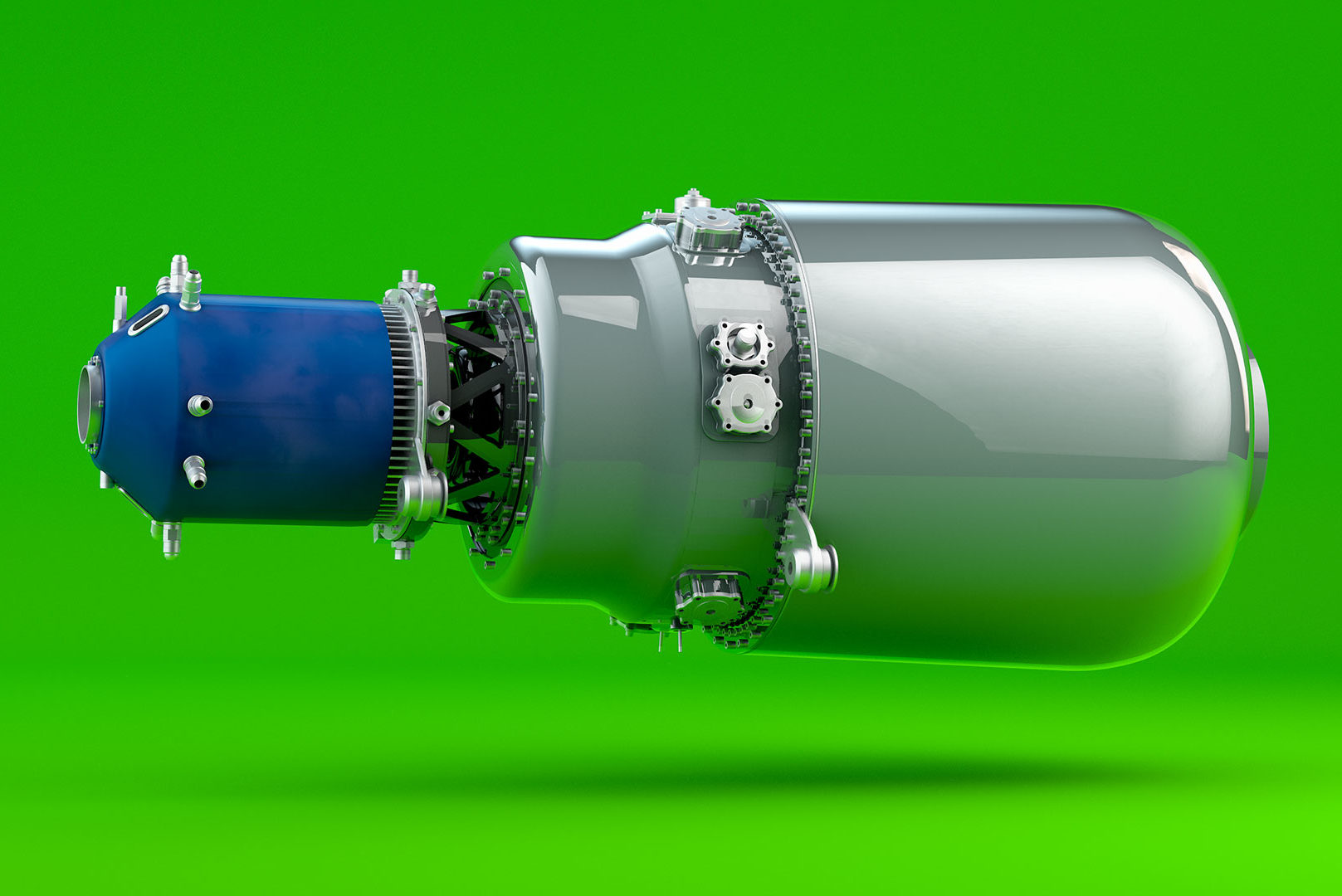
Turbotech’s TG-R90 turbogenerator (shown) is based on its TP-R90, which began testing in January. (Turbotech)
The Turbotech turbogenerators have a very high power-to-weight ratio thanks to a clever and innovative design. The electric generator drives at the same speed as the turbine, eliminating the need for a gearbox and saving additional weight. In addition, the generator is entirely air-cooled. A fan is installed inside the generator, and is also driven directly by the turbine shaft, turning at 90,000 rpm to draw air into the aluminum generator housing. The air’s path is designed to push it through a guide vane, cooling the stator and rotor, before it exits through the gaps between the enclosure’s fins.
Turbotech is currently developing and testing this technology with 55 kW (TG-R55) and 90 kW (TG-R90) power-class generators. The TG-R55 turbogenerator weighs 121 lb (55 kg) and provides 55 kW of continuous power. The turbine, equipment and fuel make up a high-power-density electric machine that weighs 254 lb (115 kg), yet carries the same energy density as 2,200 lb (1,000 kg) of lithium-ion batteries. Used in conjunction with battery power, it can provide up to 10 times more range than an all-electric aircraft. It consumes an economical 4–6 gallons (15–22 liters) of Jet-A1 fuel per hour at cruise. Turbotech says its turbogenerator can burn Jet-A1, diesel or biofuels, and may also be adapted to run on hydrogen for emissions-free flight.
Turbotech notes that several turbogenerators can be installed in parallel, enabling an increase in continuous power supply, with two TG-R90s providing 180 kW, three providing 270 kW, etc. “This architecture will allow [us] to improve safety thanks to redundancy, and optimize fuel consumption in running only the exact number of turbogenerators needed at their best power ratio,” Turbotech stated.
Both TG-R55 and TG-R90 are running on test bench this year, and are available for sale as prototypes. Turbotech has also been testing its TP-R90, which is a regenerative turboprop engine. The turbine and heat exchanger are used for both the turbogenerator and the turboprop: for one it drives an electrical generator, for the other, it drives a gearbox and a propeller.
Horizon Aircraft
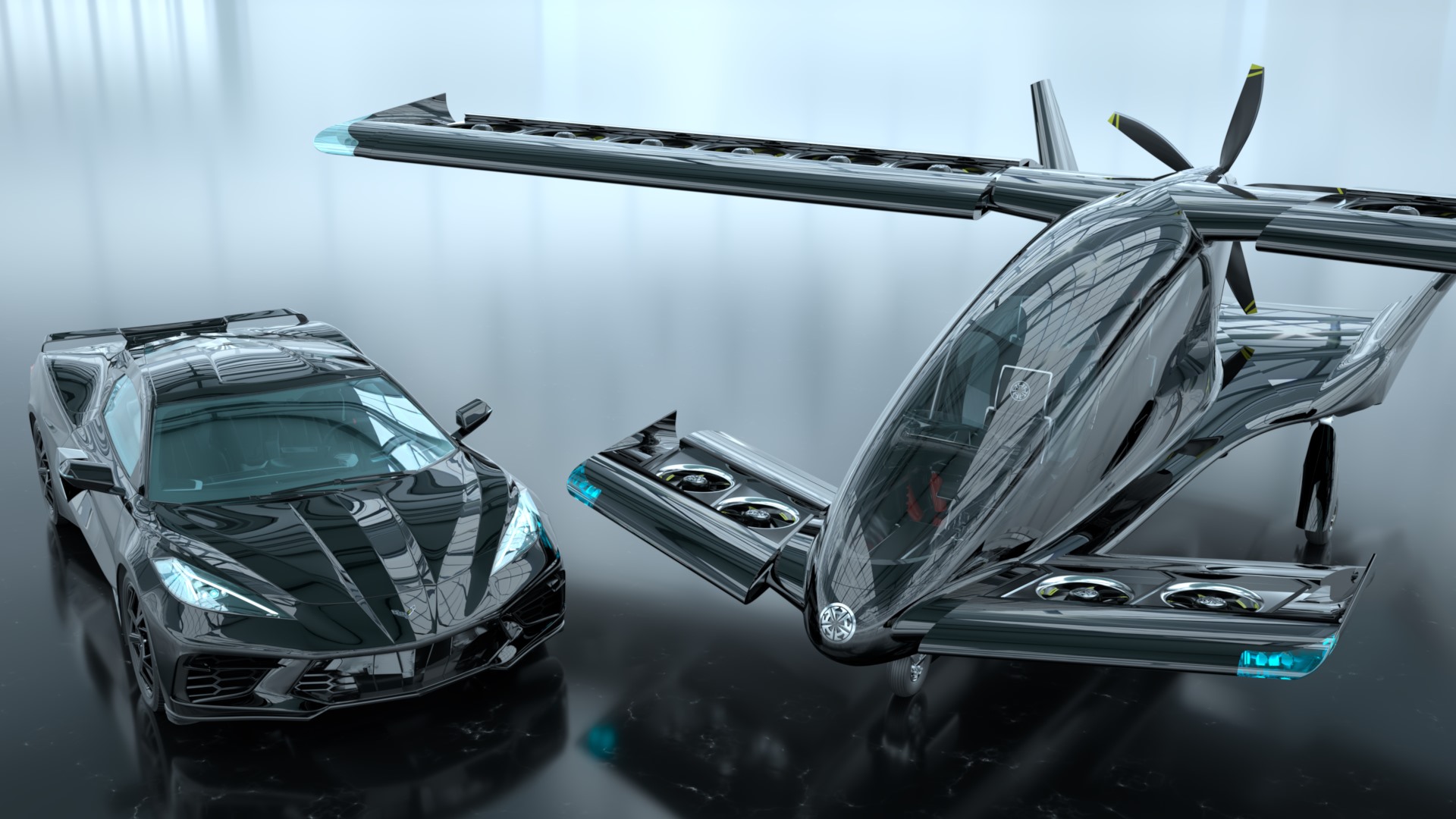
The Horizon X5 is planned to use the latest high-performance Corvette L5 engine. (Horizon)
Many eVTOL designs rely on hybrid-propulsion as a result of the limited power density of current battery technology. Lindsay, Ontario, Canada-based Horizon Aircraft had previous experience with adapting the General Motors Corvette engine for use on a 1946 Republic Seabee seaplane. Horizon is planning to use the Corvette’s gasoline-powered LS V8 engine with a smaller battery system for extended range beyond what a pure electric configuration would allow. Horizon announced in February that it was being acquired by Texas-based Astro Aerospace to help fund its Cavorite X5 fiveseat eVTOL (see “Electric VTOL News,” Vertiflite, March/April 2021). In March, Horizon announced that it had completed 200 test flights of the 1/6th-scale demonstrator.
Hard-Core Hybrids
Vertiflite | May/June 2021
Fuel-burning engine-generator sets offer choices of efficient power schemes and extended endurance for eVTOL vehicles. This round-up highlights some of the current plans and progress.
Fuel-burning engine-generator sets offer choices of efficient power schemes and extended endurance for eVTOL vehicles. This round-up highlights some of the current plans and progress.
Numerous electric vertical takeoff and landing (eVTOL) designs rely on hybrid electric propulsion to offset the limited power density of current battery technology (see “Halfway to Paradise?” Vertiflite, Sept/Oct 2020). Hybrid-electric solutions now under development maximize design freedom by using reciprocating or turbine engines to drive generator sets to power distributed electric propellers or fans. Hybrid architectures can recharge batteries for quiet flight or battery-augmented takeoffs.
VerdeGo Aero
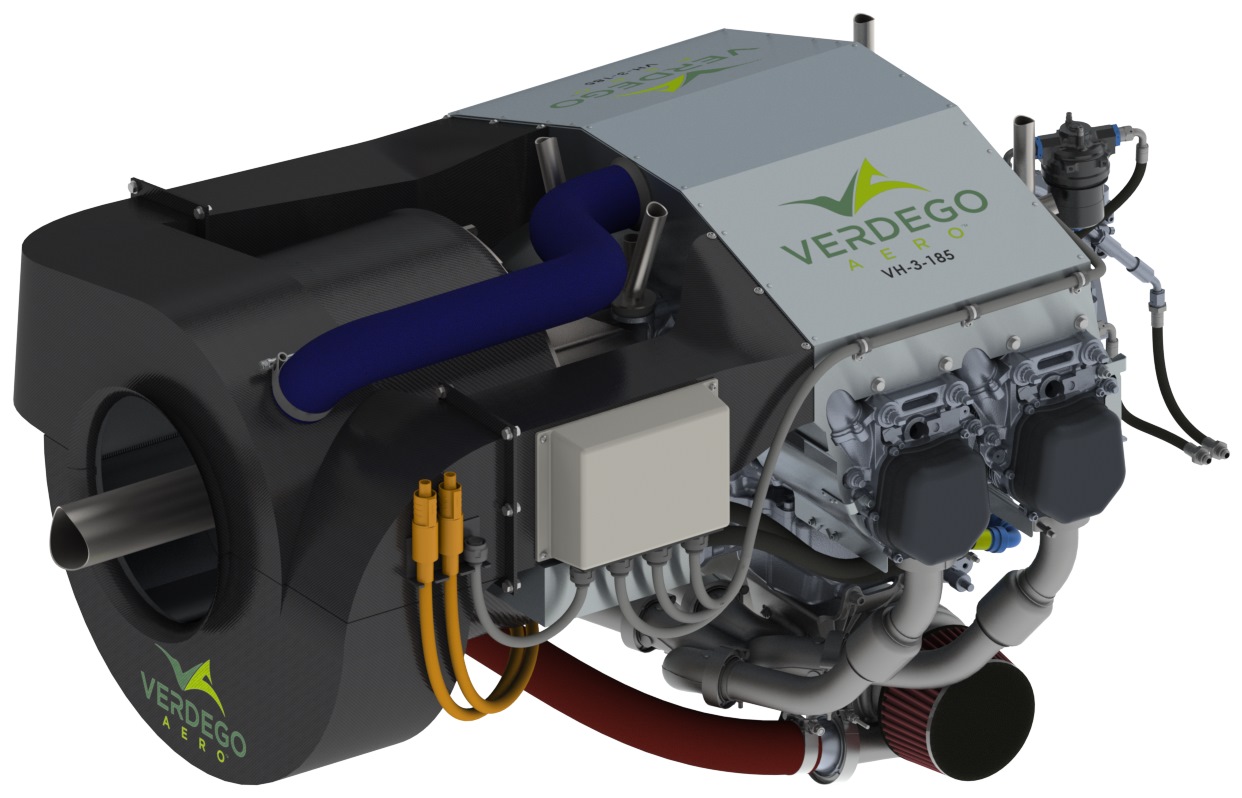
VerdeGo’s VH-3-185 hybrid-electric propulsion package will be available in a direct-drive package or with a mechanical output shaft and clutch to accommodate series and parallel operating modes. (VerdeGo)
In March, VerdeGo Aero in Daytona Beach, Florida, revealed details of its third-generation hybrid-electric propulsion system for serial and parallel applications in electrified aircraft. The VH-3-185 hybrid generator set integrates a modified four-cylinder, 230-hp (170-kW) Röder reciprocating engine with a customized generator/motor, control electronics and cooling systems to provide 185 kW output power. The generator set has a dry weight around 650 lb (295 kg) and can be paired to provide two completely parallel systems with 370 kW combined output. “It positions us in a nice design space where we have a much higher equivalent energy density than the best battery packs on the market,” said VerdeGo Aero CEO Eric Bartsch.
The hybrid-electric propulsion package will be available in a directdrive package or with a mechanical output shaft and clutch. “There are a lot of different operating modes,” noted Bartsch. “The simplest one is to just use it as a source of electrical power and route that power out the bus to motors elsewhere on the aircraft. That’s most common.” Bartsch added, “What we’ve found is there are some customers who have a main propulsion unit, a propeller or a rotor overhead, where a lot of power needs to go… The output shaft could split the power from the piston engine to a main propeller or rotor while the generator powers a distributed electric propulsion array.”
Aircraft designers could shut down the motor and drive the generator with a battery pack alone or draw on combustion engine and battery power simultaneously to provide 370 kW burst power for takeoff and drop down to battery power for greatest cruise efficiency. The new engine-generator set is largely air-cooled but includes a small, self-contained liquid cooling system. “From the airframer’s perspective, it’s an air-cooled system,” explained Bartsch. A purpose-built control system governs the generator, power-distribution electronics and cooling system. “We’re able to deliver very consistent power output [and] maintain consistent voltage with the control architecture we’ve got. What’s important is to have a highly reliable source of energy that can interact well with the battery pack, so you’ve got a fully hybrid system.”
VerdeGo Aero plans to certify the hybrid-electric generator set under US Federal Aviation Regulations (FAR) Part 33 rules governing stand-alone piston and turbine engines. “That obviously simplifies certification of the [customer] aircraft because you’re using a known quantity for the engine.” Current plans begin with the first pre-production units delivered for early-adopter flight testing within 18 months to two years. Low-volume production to support customer flight testing and non-certified applications will run in parallel with US Federal Aviation Administration (FAA) certification testing using fully conformal hardware.
VerdeGo Aero will integrate the new generator sets in its own production facilities at a site to be announced. “We will make the final unit,” said Bartsch. “Röder is the vendor for the diesel engine that’s inside. We have [a research and development] facility now where we’re doing low-volume production.” The VH-3-185 uses the SR305 engine, created by SMA Engines (Société de Motorisations Aéronautiques) in 1997, located in Bourges, France. The company was acquired by Safran in 2005, but sold to Egelsbach, Germany-based Röder Präzision GmbH in September 2020.
VerdeGo Aero found that most electric aircraft programs prioritize lower cost of ownership, reduced noise and better efficiency. “You need a hybrid that can operate quietly,” noted Bartsch. “Small turbines are expensive, loud and burn a lot of gas.” VerdeGo Aero chose a previously aircraft-certified diesel-cycle engine for its attractive power-to-weight ratio and compatibility with common jet fuels. “Of course, this hybrid system is going to be used in the general market for electric aircraft, so emissions are important,” said Bartsch. “Compatibility with jet fuel gives us compatibility with all the biofuel alternatives that are available. We want to be sure future carbon-neutral fuel sources are compatible with the VH-3.”
The VH-3-185 is VerdeGo Aero’s third-generation hybrid generator set, progressing from iron bird research tool to low-volume preproduction system to production and certification hardware. Bartsch said, “You can basically think about it as each time we went forward, we cut the weight and size in half and increased the power output.” The company is working with the FAA defining Part 33 and equivalent requirements.
Bartsch observed, “In order to get the full benefit of a hybridelectric aircraft, it’s important [that] the aircraft design leverage the new powerplant, either with distributed propulsion, active aerodynamics or all manner of things you can do with that electricity.” He noted that retrofits or conversions of traditional aircraft are not terribly attractive markets for hybridization. “You can make it fly and make it work. [But] it doesn’t make the aircraft better… I think a vertical takeoff aircraft where you’ve got eight propulsors instead of one, that’s something you can’t do with conventional propulsion. Those are great examples of where you’d like to have something like the VH-3.”
General Electric
Meanwhile, turboshaft engine manufacturers are also developing solutions for hybrid-electric aircraft. GE Aviation’s Catalyst turboprop engine is nearing flight tests on a modified Beechcraft 350 King Air. Called “the first new, clean-sheet turboprop developed for the Business & General Aviation market in more than 30 years,” the Catalyst can produce 850–1,650 shp (630–1,230 kW). The company has said that installing a permanent magnet generator in lieu of the propeller would create a 1-MW hybrid-electric powerplant for advanced air mobility solutions, such as electric vertical takeoff and landing (eVTOL) aircraft. The Catalyst was selected by XTI Aircraft as the engine for its Trifan 600 (see “XTI Aircraft’s TriFan 600 Development Continues,” Vertiflite, March/April 2020).
Honeywell
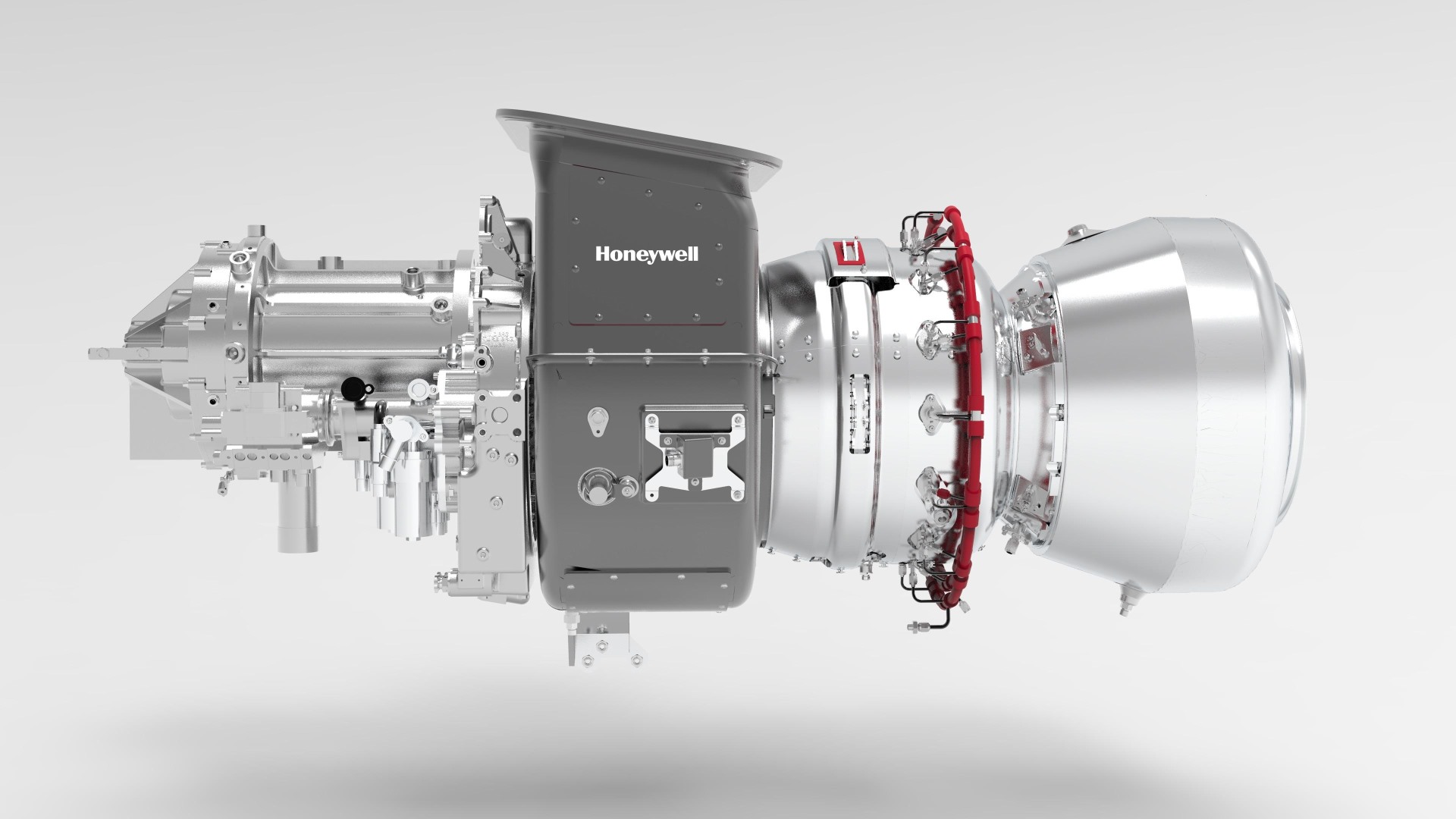
Honeywell announced its 1-MW generator, based on the HGT1700 auxiliary power unit, in March. (Honeywell)
Honeywell Aerospace announced that it is developing a power source for hybrid-electric aircraft, planned for demonstration later this year. “At 280 pounds [127 kg], the Honeywell 1-Megawatt generator weighs about the same as a motor scooter but delivers enough energy to power an entire neighborhood block,” the company said in a March 8 press release. This generator is combined with the Honeywell HGT1700 auxiliary power unit, currently flown on every Airbus A350 XWB, to form a turbogenerator 2.5 times more powerful than the version the company unveiled in 2019. That system was based on the company’s HTS900 engine with two generators, each providing 200 kW of power.
In December, Honeywell signed a memorandum of understanding with British startup Faradair Aerospace to collaborate on systems and a turbo-generation unit that will run on sustainable aviation fuel to power Faradair’s Bio Electric Hybrid Aircraft (BEHA). Faradair intends to deliver 300 hybrid-electric short takeoff and landing (eSTOL) BEHAs into service by 2030. Honeywell says it is in advanced discussions with several other potential turbogenerator customers, working to help define power requirements based on mission profiles required by various manufacturers.
LaunchPoint EPS
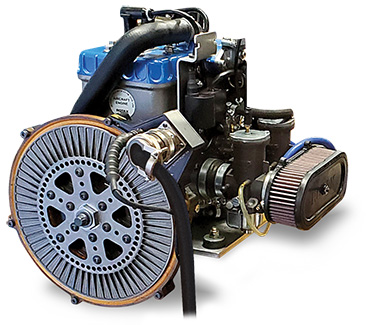
LaunchPoint’s HPS400 uses a Rotax engine to generate 40 kW. (LaunchPoint)
Goleta, California-based LaunchPoint Technologies, which has been developing power-dense Halbach-array electric motors since 2009, spun off a hybrid-electric propulsion company last year. LaunchPoint Electric Propulsion Solutions, Inc., is commercializing the motors, hybrid-electric generator sets and control software developed by LaunchPoint, as well the Modeling Advanced Aircraft Propulsion (MAAP) software, which can be used for designing electric aircraft propulsion systems. LaunchPoint was an Uber Elevate partner; MAAP was developed with support from NASA, Uber Elevate and Elevate-airframe developer, Hyundai.
LaunchPoint EPS is supplying motors and hybrid gensets for electric flight solutions in the unmanned air vehicle, aerospace power generation and advanced air mobility markets. The company originally developed small 6-kW and 40-kW hybridelectric power systems to extend the flight times of unmanned aircraft. It has already supplied several 40-kW HPS400 gensets, based on the Rotax 582 engine, to potential customers.
The company says its patented lightweight, efficient, power dense, air-cooled motors and gensets range from 1.5 kW to 250 kW.
Pratt & Whitney
Like other major engine companies with turboshaft products, Pratt & Whitney Canada is also exploring hybrid-electric solutions. It had planned an ambitious hybrid-electric airliner demonstration under what it called Project 804. Revealed in 2019 under the former United Technologies Advanced Projects (UTAP), it also included Collins Aerospace and Pratt & Whitney Canada, which were then also part of United Technologies Corp., and now all are part of Raytheon Technologies. Project 804 is developing a 1-MW hybrid propulsion system, with the intent to replace one of a De Havilland Canada Dash 8-100’s turboprops.
Raytheon said last summer that the project had been slowed by the COVID-19 pandemic and its impact on civil aviation, which prompted the elimination of some 20,000 jobs across the company.
Rolls-Royce
Rolls-Royce is working with APUS, an aviation engineering company based in Strausberg, close to Berlin, and the Brandenburg University of Technology (BTU) in Cottbus, in developing a hybrid-electric electric conventional takeoff and landing (eCTOL) demonstrator, using Rolls-Royce’s legacy Allison 250 turboshaft. The hybrid-electric M250 could be used across a range of transport platforms to enable distributed electric propulsion, including eVTOL, for power requirements from 500 kW to 1 MW. Rolls-Royce purchased the electric and hybrid-electric aerospace propulsion activities of Siemens in 2019.
Safran and Airbus
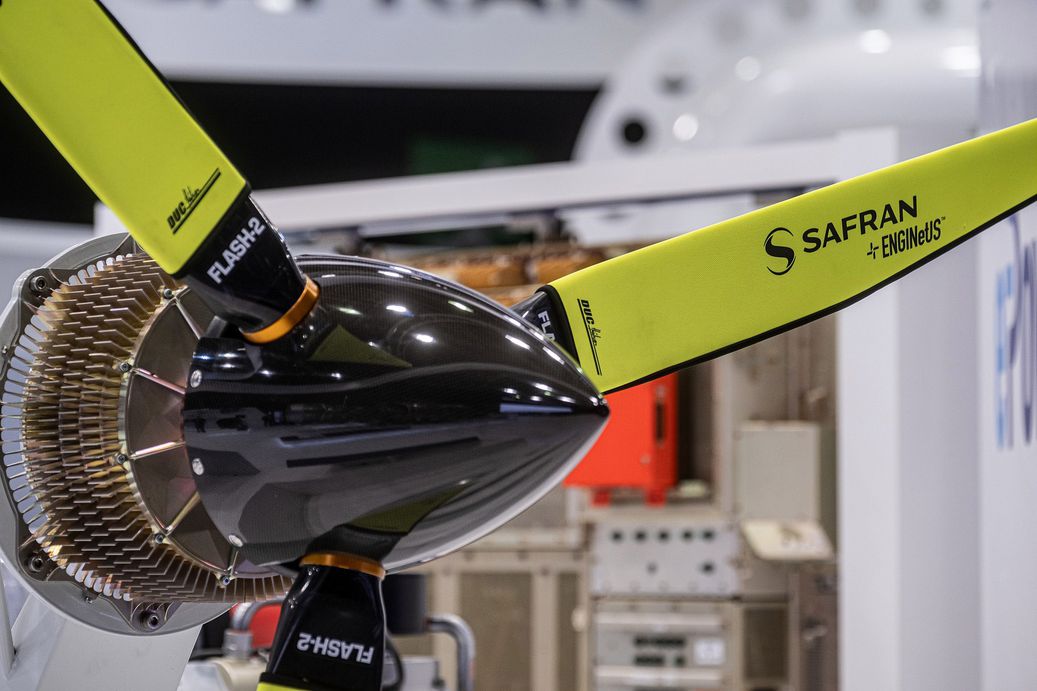
The 50-kW Safran ENGINeUS will be used on the Daher-Safran-Airbus EcoPulse hybrid-electric demonstrator. (Safran)
In July 2018, Safran Helicopter Engines announced it had ground tested its first distributed propulsion system, which generated 100 kW of electrical power, at its facility near Pau-Pyrenees Airport, France. Since then, it has developed a number of technologies for hybrid-electric eVTOL and eSTOL applications.
Safran was selected for Bell’s original hybrid-electric Nexus 6HX eVTOL air taxi, as well as the VoltAero Cassio 1 and the Airbus-Daher EcoPulse Demonstrator eSTOL aircraft. In December, Safran, which is responsible for EcoPulse’s distributed hybridelectric propulsion system, announced it had finalized the technical configuration of its six electric thrusters. They will be fitted with 50 kW ENGINeUS 50 electric motors with integrated electronics and patented air. The Safran ENGINeUS motor will be submitted for certification by the European Union Aviation Safety Agency (EASA) using the same basis as granted for a turboshaft engine. The ENGINeUS 100 will also be certificated by the US FAA on the Bye Aerospace eCTOL eFlyer 2 and eFlyer 4.
Safran is also providing the 2,500-shp (1,860-kW) Aneto-1X engines for the Airbus Racer high-speed compound helicopter. For its “Eco Mode” configuration, one engine can be “paused” and brought to flight idle, for a 15% fuel savings. Whenever needed — during acceleration, landing or autorotation, for example — the idling engine is rapidly and automatically restored to full power using an innovative high-power-density electric motor.
Meanwhile, Airbus provided an update in March on what it calls Europe’s largest facility dedicated to alternative propulsion technologies — its E-Aircraft Systems House, which was launched in 2016. It has two distinct facilities: one for testing mediumvoltage systems appropriate for rotorcraft and eVTOL aircraft, and one for high-voltage testing for larger, commercial aircraft. The medium-voltage facility has been used for the Racer and the CityAirbus eVTOL demonstrator since 2018.
Turbotech
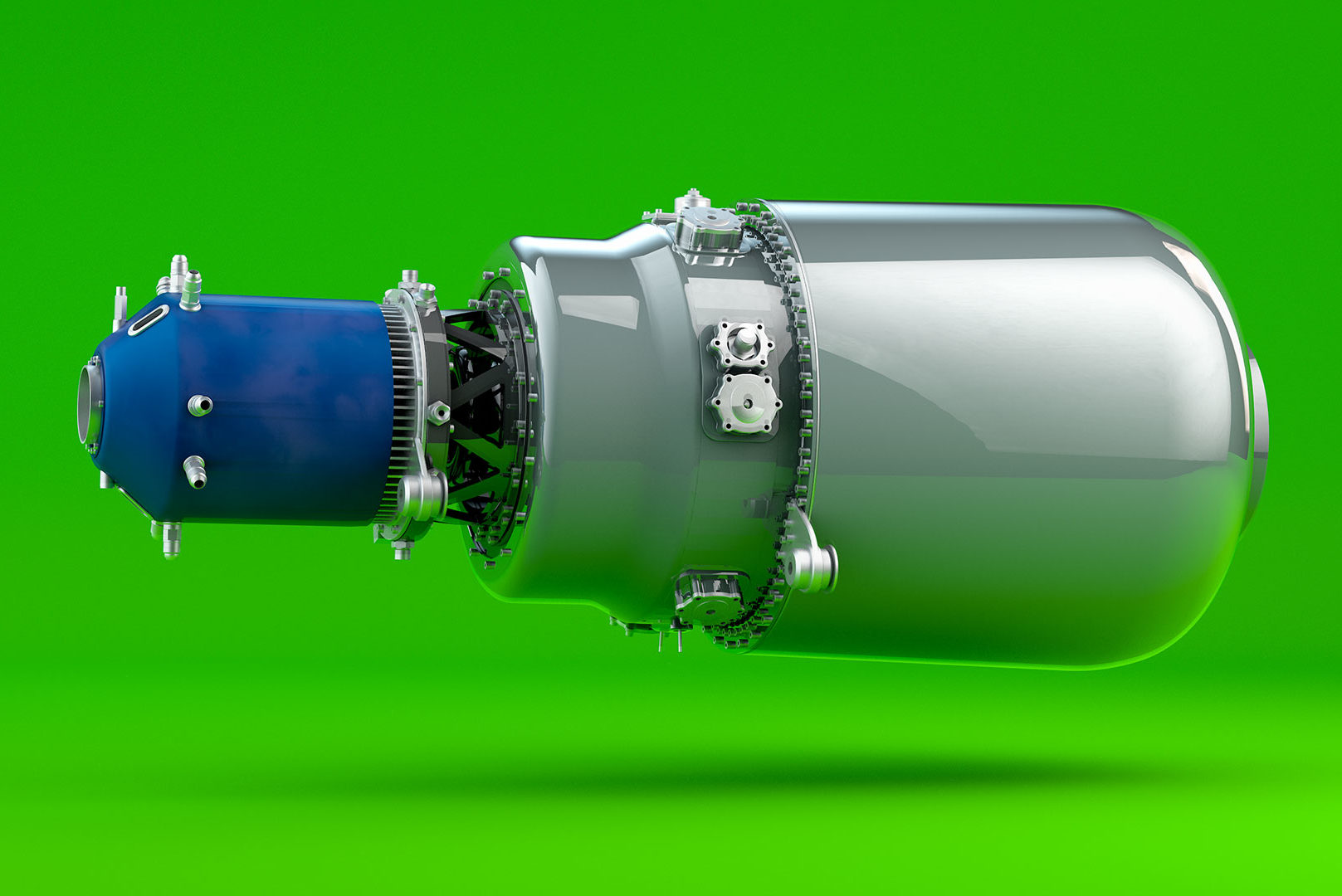
Turbotech’s TG-R90 turbogenerator (shown) is based on its TP-R90, which began testing in January. (Turbotech)
The Turbotech turbogenerators have a very high power-to-weight ratio thanks to a clever and innovative design. The electric generator drives at the same speed as the turbine, eliminating the need for a gearbox and saving additional weight. In addition, the generator is entirely air-cooled. A fan is installed inside the generator, and is also driven directly by the turbine shaft, turning at 90,000 rpm to draw air into the aluminum generator housing. The air’s path is designed to push it through a guide vane, cooling the stator and rotor, before it exits through the gaps between the enclosure’s fins.
Turbotech is currently developing and testing this technology with 55 kW (TG-R55) and 90 kW (TG-R90) power-class generators. The TG-R55 turbogenerator weighs 121 lb (55 kg) and provides 55 kW of continuous power. The turbine, equipment and fuel make up a high-power-density electric machine that weighs 254 lb (115 kg), yet carries the same energy density as 2,200 lb (1,000 kg) of lithium-ion batteries. Used in conjunction with battery power, it can provide up to 10 times more range than an all-electric aircraft. It consumes an economical 4–6 gallons (15–22 liters) of Jet-A1 fuel per hour at cruise. Turbotech says its turbogenerator can burn Jet-A1, diesel or biofuels, and may also be adapted to run on hydrogen for emissions-free flight.
Turbotech notes that several turbogenerators can be installed in parallel, enabling an increase in continuous power supply, with two TG-R90s providing 180 kW, three providing 270 kW, etc. “This architecture will allow [us] to improve safety thanks to redundancy, and optimize fuel consumption in running only the exact number of turbogenerators needed at their best power ratio,” Turbotech stated.
Both TG-R55 and TG-R90 are running on test bench this year, and are available for sale as prototypes. Turbotech has also been testing its TP-R90, which is a regenerative turboprop engine. The turbine and heat exchanger are used for both the turbogenerator and the turboprop: for one it drives an electrical generator, for the other, it drives a gearbox and a propeller.
Horizon Aircraft
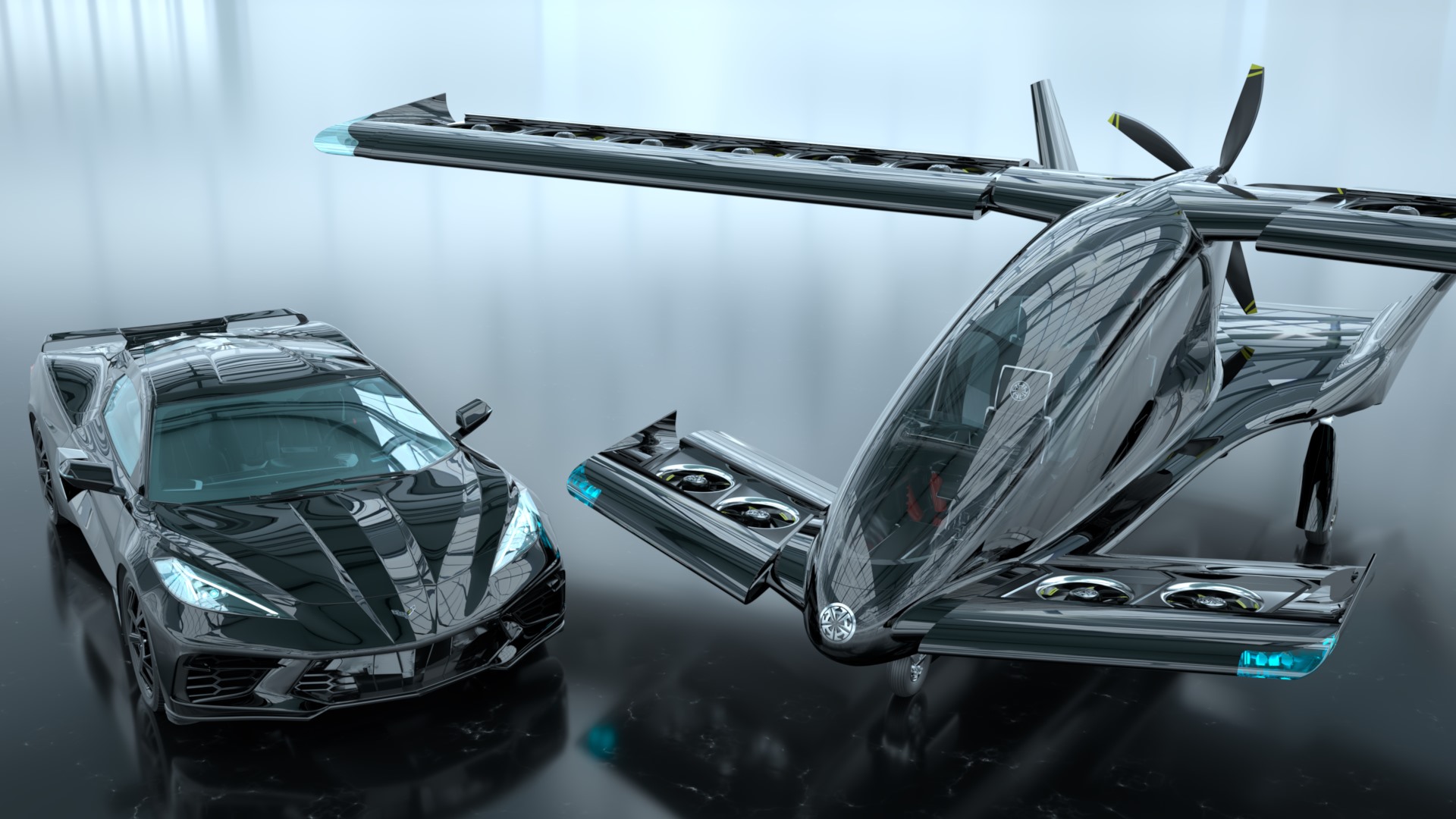
The Horizon X5 is planned to use the latest high-performance Corvette L5 engine. (Horizon)